Table of Contents
Clinchers; Tubes and Tubeless
In the early 21st century, the most common bicycle tires are pneumatic clincher or bead clincher tires. The tire has a bead, formerly made of metal wire. Modern tires are manufactured with material that can rebound into a circle after being folded for packaging and shipment. The tire contains an inner tube, which is soft and vulnerable to punctures and tears. Clincher wheels curve into a bead hook at the rim to catch and hold the bead. In tubeless wheel, the rim has
- a central groove which can be described as a valley or well;
- a rim strip to seal the spoke holes
- bead channels – the spaces between
- a shelf, between the rim wall and the well, and
- a bead hook.
Tubeless tires are clincher tires sealed and inflated directly – no inner tube. Tubeless systems generally require sealants installed in the tire; tubeless tires are supposed to self seal to mitigate small punctures. Riders may carry inner tubes to install a tube in a tubeless tire to mitigate a larger puncture. A tubeless tire bead is designed and manufactured to fit into tubeless wheel rims. A tubeless or tubeless ready wheel has a machined bead channel. The beads and the rim channels are supposed to fit tightly enough to be air tight when the tire is inflated. The seal is normally obtained by applying tire sealant to the edge of the side walls along the bead.
The wheels on my 2019 Topstone are “tubeless ready” WTB i23, a metal alloy with a 23 mm rim; the 23-622 model. (WTB has versions of i23 including a “26 inch” mountain bike rim, and i23 (23-622) for 700c tires from 700c x 32 to 700c x 46). The 23 mm measurement is taken between the rims in the bead channelat bead seat. The tires were “tubeless ready” WTB Nano 700c x 40. Some manufacturers (e.g. Mavic) manufacture rims and tire beads to the Uniform System Tubeless (UST) standard. The bead seat is designed to accept and hold the beads of UST tires without tape. WTB’s tubeless metal rims are sealed with plastic rib tape (liner) which adheres to the rim. The rim channel and wheel beads are beadlock – which is WTB’s way of saying manufactured to the UST standard. WTB, like other manufacturers, calls tubeless tires a modern improvement or feature and calls its beadlock system a feature. It is hard to unmount a tubeless tire from a rim to replace a tire or to fix a flat. It requires a skill that has to be learned. It can be a problem with some wheels and tires as noted in this YouTube review of the Topstone (at the end of the 3 minute video). I
Tire sizes are normally described by height. Height is the diameter across the wheel on the outside of the tire, measured on the mounted and inflated tire. The height is the nominal exterior diameter of the tire, which was used by manufacturers of tires and other components. 700c was the term used in a French system. The height, assuming the tire is a perfectly round torus, should be the diameter of the rim plus the 2 x the diameter of the tire. For 700c x 28, this works out to 678 mm which is almost 28 inches (700 mm. = 27.559 inches) . The tire, inflated, has an irregular oval cross section, sort of egg or pear shaped. Diagram below. A tire is always marked with a tire size in a nominal diameter system, and a size in the International Standards Organization ISO or ETRTO system. The most common tires on gravel and all-road bikes are 700c tires – considerably fatter than 700c road bike tires. 700c is a standard for tires with a nominal outside diameter around 700 mm (28 inches). There are skinny 700c x 25 (ISO 25-622) tires and fatter 700c x 36 (ISO 36-622) tires. The 622 in the ISO descriptions of 700c tires refer to the 622 mm diameter of the wheel.
700c (ISO 622) is also the standard for describing larger “niner” and “niner +” (29 inch x 2+ inch) wheels. 650b is a standard for tires with a nominal diameter around 650 mm (27.5 inches). The ISO descriptions of 650b tires refer to the 584 mm diameter of the wheel and the tire.
The other number in the nominal diameter or ISO description is the bead seat diameter (“bsd”) – the width measured across the tire or the rim at at the inner bead seat where the tire bead fits into the bead seat of a wheel. The width is usually the same in the nominal diameter and ISO systems. There are some outliers. A tire may be 700c x 38 and 622-40.
A higher bsd means a fatter tire, mounted and inflated, with a larger diameter and circumference than a narrow tire. The actual thickness (width from sidewall to sidewall, from the outside)≥ bsd. Actual thickness varies, depending on pressure and load. For higher bsd numbers, the thickness starts to push out. Height (outer diameter) and thickness can vary slightly depending on the construction and inflation of the tire. The height and thickness of some tires:
Tire Size | ISO | Circumference ≅ | Diameter (C/π ) | Thickness | Source | |
700c x 18 | 18-622 | Generic/Standard | 2070 mm | 658 mm | ||
700c x 25 | 25-622 | Generic/Standard | 2111 mm | 672 mm | ||
700c x 28 | 28-622 | Generic/Standard | 2130 mm | 678 mm | ≅ 28 mm | |
650b x 50 | 50-584 | Generic/Standard | 2149 mm | 684 mm | ||
700c x 38 | 38-622 | Generic/Standard | 2180 mm. | 694 mm |
Clearance
The rear tire has to fit between the chain stays behind the bottom bracket and between the seat stays below a bridge below the seat. The bottom bracket shell accomodates a bb and a crank with a suitable Q factor. On the Topstone, the chain stays are straight and parallel to each other for a few cm behind the bottom bracket. The distance between the chain stays is about 56 mm in the parallel section where a 700c tire would have to fit. The The seat stays are straight and bend out to fit around the rear axle assembly (cassette and disc brake rotor). The distance between the seat stays is 66 mm where the tire runs. The front tire has to fit between the fork blades under the fork crown. The distance between the fork blades where a tire runs is 61 mm or more. (The measurements were made with a caliper with the wheels on the bike). The side clearances allow 700c x 40 mm tires. The clearances at the tops of the tires under the seat stay bridge and the front fork crown were tighter. The WTB Nano 700c x 40 tires were too big to allow for fenders. For subsequent model years, Cannondale shipped the Topstone with 700c x 37 WTB Riddlers, a slightly smaller and narrower tire (with small knobs).
The WTB Nano tires had a mountain bike type tread. The tread on the center line of the tire was made up of chevron shaped groups of cleats or knobs. There were alternating gaps in the chevron. I thought the tread caused vibration, noticeable at low speeds; experienced gravel riders reviewing it thought it made for a smooth ride. I agreed it was smooth unless speed dropped to under 12 km/h. I did not need cleat or knobs e for my riding on asphalt and packed gravel. I downsized the tires to 700c x 38 Panaracer GravelKing SK tires.The dense small knobs were smooth to ride, although I expect some drawbacks.
Some all-road and gravel bikes can be adapted to use 650b wheels and tires. The 650b standard is based on a 584 mm. diameter wheel. A 650b x 48c (ISO 48-584) wheel is as tall as a 700 x 28c. It has more rubber, and is wider and heavier. 650b x 48 is not as tall as a 700c x 38; it will fit into the fork under the fork crown and the seat stay bridge. René Herse states that its 650b x 42 tire is 41-43 mm wide, and its 650b x 48 is 49-50 mm wide. These tires will fit within the clearances in the Topstone, but fitting a 60 mm diameter fender for 48 mm tires would be awkward.
Fenders
Fenders were normal part of the design of all-purpose bikes used by commuters and city riders, and installed by manufacturers for most of the 20th century. Road bikes, imitating racing bicycles, were built without fenders or even mounting points for fenders. While fenders were useful for some uses of mountain bikes, fenders were hard to design. manufacture and install. Fenders for road bikes, hybrids, and mountain bikes became accessories. Fenders were more popular on touring bikes and endurance/randoneusse bikes.
To fit fenders, the rider needs to know the thickness of the tires, and the clearances in the bike frame. The front fender has to attach to the fork at or near the fork crown. The rear fender needs to attach to the frame behind the bottom bracket between the chain stays, and at a bridge between the seat tubes. The attachments at those points support the front parts of the fender in the proper position. Fenders stays hold the back parts of the fenders in position. Fender stays normally attach to the frame and the fork near the axles.
A fender should fit around an inflated tire, with horizontal and vertical clearance. The exterior diameter of the fender, measured across the base of the arc of the fender indicate that the fender needs that horizonal distance to fit between the seat stays or fork blades without cutting or bending the fender Velo Orange, a manufacturer of aluminum fenders, suggests an 8 mm. horizonal difference between the exterior diameter of the fender and the bead seat diameter of the tire. This suggests a 700 x 40c tire needs a 48 mm exterior fender. A fender should clear the tire vertically (along the radius of the circle) by about 20 mm where the fender covers the tire. There has to be a vertical gap of more than 20 mm from the inside of the fork crown or the seat stay bridge and the outside of the tire.
My first fenders for the Topstone were SKS P50 Chromoplastic Longboard Fenders, a popular model sold in many shops and online stores in the USA and Canada including Modern Bikes and Universal Cycles. SKS marketed these fenders as wide enough to cover 700c tires in the range from 700c x 38 to 700c x 45. The P50 fenders had an exterior diameter of 50 mm. Plastic is light but it is prone to twisting and vibration. The rear ender mounted easily to the eyelet between the chain stays behind the bottom bracket. SKS, like other fender manufacturers provides a fender bridge that has to be bent around the outside of the fender and crimped around the edges. This bridge has to be centered on the fender to align to the frame mounting fitting on a bridge between the seat stays, slid into position and crimped onto the fender. If this is not done successfully, the fender will be twisted out of true. There is very little margin for error . SKS chromoplastic fenders use V shaped stay ; each stay has 2 arms. These stays are designed to attached to eyelets at the ends of the chain stays. The stays did not quite line up to eyelet . I had to adapt some left over parts from a rack mount kit to fabricate little fins. I had to bend the stays out to balance the tension to keep the fender from rubbing, but it worked.
The front fender fit under the fork crown and appeared to have adequate clearrance over the tire, but did not clear the original 700c x 40 knobby/cleated WTB Nano tire. I downsized the tires. The next problem with those fenders was the lack of eyelets for fender stays at the ends of the fork blades. The only eyelets stays are on the inside of the fork, 15 cm above the end of the fork. This was not a good place for the SKS breakaway tab or for a V shaped stay. I was able to improvise an attachment for the SKS break-away fender stay mount, and bend the V arms of the stays to slide into the attachments on the fender. This worked for my rides in the winter of 2020-21. I began to get a rubbing noise at higher speeds on chipseal. The V stays did not support the plastic fender under those conditions.
Riders reported installing SKS plastic fenders on Cannondale road bikes in forums, Reddits and YouTube, but these riders referred to bikes with eyelets at the end of the fork blades. One English rider reported, in a YouTube video, using the Bontrager NCS plastic fenders on a Topstone with carbon forks. That fender has a single straight (adjustable) stay, which normally attaches to an eyelet at the end of fork blade, but can be attached to the eyelets on the Toptone. I installed aluminum Velo Orange fenders. These are light but rigid, and attach with a single stay on each side of the fender. This is how the stays fit, using the pre-drilled holes for the stay:
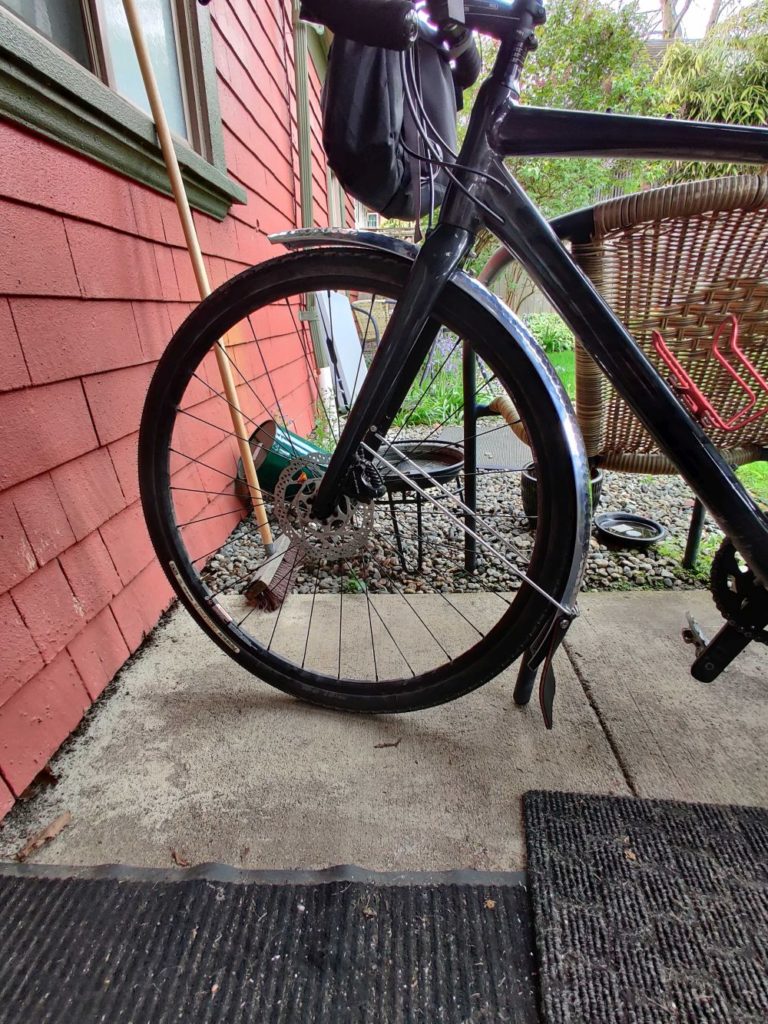
Carbon Fiber Fork
Carbon fiber forks are offered on many production road and gravel bikes with steel or aluminum alloy frames. A carbon fiber fork is light and stiff, which is supposed to improve steering, although this can be debated. A carbon fork on bike with disc brakes has to be stiff. A stiff fork does not dampen vibration. Many carbon forks lacks eyelets for racks and other devices, which limits some uses of the bike. The carbon composite must be laid over a metal component tapped to receive a bolt and act as an eyelet. This is tricky and expensive.
Crankarms and Cassette
I changed the stock 172.5 mm crankarms to 165 mm – a shorter radius and less stress on knees. I replaced the Shimano 105 11-32 cassette for an SRAM PG-1170 11 cog 11-36 for a couple more low, climbing gears. With the 30 tooth front ring, this change gives me 30×36 as the lowest gear.